
A Solution for Terpene Odors from ‘Green’ Facilities
Titan Consulting, an engineering consulting company, requested a new method be designed for filtering the terpene odor produced in cannabis grow facilities, preventing odors from escaping premises.
Currently, the main air filtration method used is non-recyclable, activated carbon air filters that only adsorb terpene odor (VOC gases) until it becomes ineffective and requires replacement every 6 months.
The client believes that it will be crucial to optimize building systems by minimizing replacement frequency and costs, boosting energy efficiency, and applying practical ‘green’ solutions as the potential cannabis sector expands in the near future. The stringent rules and regulations established on the cannabis grow facilities are another factor driving this development.
“The building or part of the building where cannabis is produced, packaged, labeled and stored must be equipped with a system that filters air to prevent the escape of odors.”
— Cannabis Regulations of Canada (SOR/2018-144), Government of Canada, Oct.17, 2018, Ottawa.
Project Requirements were formulated prior to conceptual design.
Swipe to see the design Functions, Objectives, Constraints, and Operating Environment analysis:
After several idea iterations, 3 designs were proposed: Thermal Reactivation of Charged Carbon Filters, Negative Ion Air Purification & Photo Electrochemical Oxidation (PECO) Filter.
The 3 designs have been illustrated below with key information and tabular reasoning of how well each design met the objectives.

Design 1 Illustration

Design 1 Objectives Performance

Design 2 Illustration

Design 2 Objectives Performance
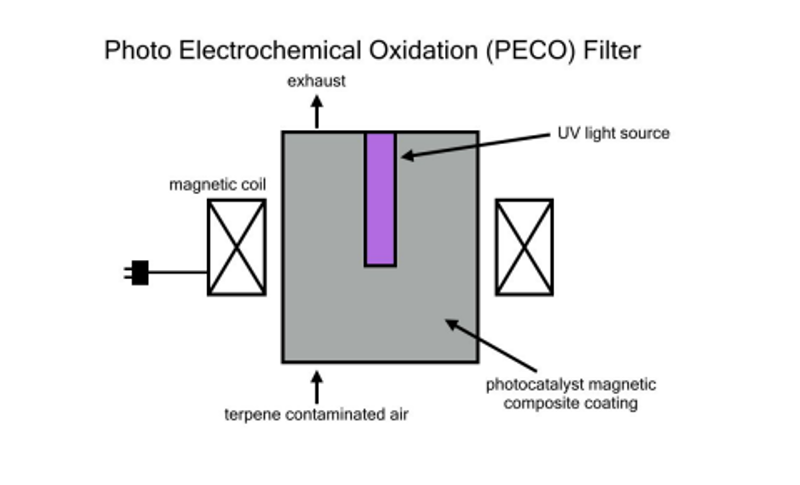
Design 3 Illustration

Design 3 Objectives Performance
After a thorough weighted decision matrix, the final scores pertaining to each Design 1, 2 and 3 were 48%, 58% and 70% respectively. Thus, the final design proposed to client was the Photo Electrochemical Oxidation (PECO) Filter.
The mechanism by which the design works is demonstrated in the steps below:
TiO2 is a photocatalyst, that is chemically bonded with Fe3O4, a magnetic material, to create a TiO2@Fe3O4 composite.
The TiO2@Fe3O4 composite is coated on the inner layer of the Aluminium casing/reactor.
The UV light inside the reactor energizes TiO2 in the composite, creating OH• free radicals.
Incoming air contains terpenes (VOC gases), which chemically react with OH• free radicals, forming CO2, H2O, and trace elements, as shown below:
Hydroxyl free radical (OH•) + Oxygen in air (O2) + Terpene (C,O,H) → Carbon dioxide (CO2) + Water (H2O) + (trace elements)
The magnetic coils are used to agitate the Fe3O4 in the composite to allow turbulent, efficient mixing of terpenes in incoming air with OH• free radicals.
3D model of design cross-section
The filter coating replacement or maintenance process that facilities could undergo with their technicians on a semi-annual basis was also developed:
Remove the UV light
Unclamp the outer casing from the top and bottom plates
Remove the casing/reactor from the ventilation
Remove the magnetic coils, then put them onto a newly coated casing
Place the new outer casing into clamped position and insert UV light
The old casing/reactor is recoated, to be used as the next replacement measure
Illustration of maintenance steps
A study was conducted that depicts how effective PECO technology is compared to Carbon filters in terms of filtering, eradicating, or removing volatile organic compounds (VOC gases), which is what terpenes are.
The graph illustrates the proportion of VOCs in a controlled environment. As you can see, since carbon only adsorbs, it can remove VOCs strongly to just under 20% before it can no longer adsorb, resulting in VOCs still being present in the environment at close to 80%. In contrast for PECO, the VOCs kept reducing till virtually all VOCs were removed.
PECO VS Carbon